Glass and transparent plastics, especially acrylic resins, have long been used in the lighting industry for various aesthetic and functional purposes. As the industry has evolved, light-emitting diode (LED) lighting has moved from niche applications to more mainstream commercial and residential use, and there has been a growing interest in plastics — especially polycarbonate — because of the properties of the material and the versatility it provides. Polycarbonate is now seen in a variety of areas in LED lighting including lenses, optics, covers, channel letters, sign facing, globes, and light diffusers.
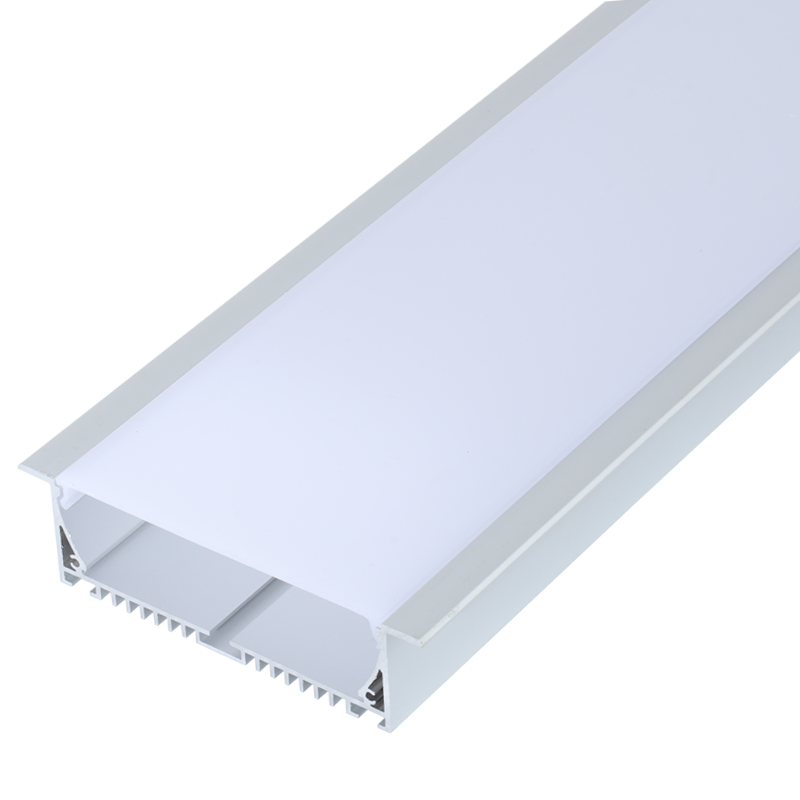
The mechanical integrity and durability of the product are the qualities that have caused the industry to focus on polycarbonate. Certain features of polycarbonate, such as heat resistance and transparency, are important in the LED lighting industry. But because the LED light source is relatively expensive to produce and can last up to ten years, manufacturers and designers are primarily concerned that the material used for the light lens, or cover, holds up for the same amount of time that the LED light source lasts — in order to protect the costly light source.

This article discusses important considerations when selecting a material for use with LED lighting solutions. It focuses on the benefits of polycarbonate and why manufacturers and molders alike consider polycarbonate to be an ideal choice to use with LED lighting.
When selecting polycarbonate, first and foremost, one needs to consider the application. How will the polycarbonate be used? How will the source be housed? Today, the uses of LED light sources are almost endless. LED lights can be seen in storefront signs and channel letters, traffic signals, recessed down lights, task lights, retail and refrigerated displays, street and area lights, LCD TV displays and monitors, mobile appliances, and many other applications. When designing covers, lenses, or optics for these varied applications, one must consider the capabilities of the materials — the durability, optical properties, thermal stability, ignition resistance, design flexibility, and UV stability. What is the environment of the LED source? What elements does it need to withstand? These are some other considerations.
DURABILITY
Durability is the starting point for light source protection, especially outdoors. What is needed is a material that is tough. Since the LED light source itself, a solid-state semiconductor, is a much more robust product than traditional incandescent light sources, the materials used to cover the source should be at least as resilient.
Polycarbonate is much more impact-resistant and is less prone to breakage than other materials available. It has outstanding toughness, even over a wide temperature range. Polycarbonate, which is used for items such as bulletproof and riot shields, aircraft canopies, and hurricane panels, can withstand tremendous impact. In general, polycarbonate resins are ten times more impact resistant than acrylics and up to 30 times more impact-resistant than glass.
Due to this outstanding toughness, polycarbonate is easier to work with and less prone to breakage or chipping when cutting the material into shapes. In many applications, it is possible to down-gauge or decrease the thickness of a fabricated part when using polycarbonate versus another material. This results in part-weight and material-cost reductions, which offer a more environmentally friendly solution due to the fact that less product is being used and a reduced amount of energy is needed.
Post time: May-08-2020